Concrete Contractors Greensboro NC can provide a number of benefits for your property. They can save you time and money by creating a detailed plan for your concrete project.
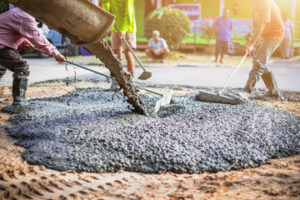
Ask about their licensing, insurance, and bonding. Also, find out if they offer a warranty. This will help you choose a reputable concrete contractor.
Concrete is a versatile construction material, able to be used in a variety of projects from foundations to sidewalks. Professional concrete contractors have specialized knowledge of the proper techniques to complete a concrete project in an efficient and cost-effective manner. While it may be tempting to save money by taking on a concrete project yourself, the costs of labor, equipment, and materials often add up quickly.
The size and scope of the concrete project has a major impact on pricing. Larger-scale projects will usually cost more per square foot than smaller-scale endeavors. However, it is important to consider the project’s function and long-term needs to find a balance between size and budget.
Skilled labor plays a significant role in the cost of concrete construction. Concrete professionals are highly trained in the placement, finishing, and curing of concrete, which contribute to the quality of the final product. Labor market conditions, overtime requirements, and union regulations can also drive up prices.
Another factor that impacts pricing is the availability of quality aggregates. The closer the construction site is to the source of aggregate, the less expensive it will be. Concrete contractors have a network of suppliers that they work with, and are able to purchase aggregate at the best price possible for their clients.
Maintaining the integrity of a concrete structure is a crucial task that requires ongoing inspection and maintenance. A quality concrete contractor will regularly evaluate the structure and identify any issues that require attention. This prevents the need for costly repairs in the future and protects the structural integrity of the structure.
The durability of concrete structures contributes to substantial savings in upkeep costs. Unlike wood, concrete is not susceptible to rot or insect infestations. It is also a more energy-efficient building material than other materials, making it a great choice for Multi-Family Residential Construction, Commercial Construction, and Single-Family Residential Construction.
Safety
Working with concrete and cement carries certain risks, so safety precautions are essential for the work. A reputable commercial concrete contractor is dedicated to providing a safe environment for their workers, which helps them avoid costly mistakes and ensures that the finished product is durable and long-lasting.
The first step in ensuring safety is to secure the work area by putting up barriers to prevent unauthorized persons and bystanders from entering the construction site. This reduces the risk of accidents involving untrained individuals. In addition, all personnel must receive proper training on the equipment and materials they will use at the jobsite, including safety protocols, lockout/tagout procedures, and proper handling of concrete and cement products.
Workers should also wear appropriate personal protective equipment (PPE), such as gloves and a dust mask, when mixing or pouring concrete. Any contaminated PPE should be washed immediately with clean water to avoid infection. Additionally, it is important to keep skin as dry as possible, since contact with wet concrete can cause chemical burns. A long-sleeve shirt and a dust mask can help prevent this from occurring, and barrier creams can be used to protect hands and arms from industrial dermatitis.
Proper lifting techniques are essential for concrete contractors, as they often have to lift heavy bags of cement and other materials. This can lead to back and other muscle strains, so workers should always remember to bend at the knees, keep their backs straight, and move the load using their legs rather than their shoulders. When it comes to moving heavy loads, mechanical and powered equipment can be used instead of manual labor to reduce the risk of injury.
Workers should hydrate regularly to stay hydrated when working in the heat, and they should take frequent breaks in shaded areas. This is critical to preventing heat-related illnesses, such as heat exhaustion and heat stroke. It is also advisable to wear sunscreen and sunglasses when working outdoors, and to avoid direct contact with concrete and cement dust, which can cause irritation to the eyes. In addition, workers should wear gloves and a dust mask when clearing concrete or cement dust, as it can irritate the nose and throat.
Durability
Concrete contractors are the professionals who turn your construction vision into a tangible reality. They craft durable foundations, paving slabs, and parking lots with precise measurements, robust materials, and an eye for design that ensures the longevity of your building project. In addition, they ensure that all building codes and regulations are followed for a safe and compliant finished product.
When choosing a contractor for your commercial construction project, look for experience. Contractors with years of industry expertise have a better understanding of the challenges that may come up during a concrete project and are prepared to resolve them quickly and efficiently. They will also be able to offer cost-effective solutions and recommend the best materials for your specific needs.
In addition to having the right skills and experience, professional concrete contractors are committed to continuing education. They will attend workshops and seminars to learn about the latest advancements in concrete technology. These innovations can affect everything from concrete mix designs to the use of admixtures. By staying up to date on these changes, concrete contractors are able to maximize the strength and durability of their work.
While many people assume that concrete is a simple construction material, it actually requires significant attention to detail to create a quality result. Concrete contractors are well versed in the proper mixing and pouring of concrete, as well as the correct methods for cutting, forming, and finishing. This includes the use of specialized tools like trowels and floats to achieve the desired texture, smoothness, and finish.
Once the concrete is poured, it must be properly cured. This process can take up to four weeks and involves maintaining moisture, adding plasticizers, and applying sealants. This is essential for the long-term integrity of the concrete and helps protect against cracks, environmental damage, and stains.
When selecting a concrete contractor for your construction or renovation project, be sure to choose one who is licensed and insured. This will protect you from liability in the event of an accident during construction. In addition, you should check the contractor’s website for a portfolio of previous projects and read public reviews on Google, Facebook, Angi, or other review sites. You should also contact the contractor directly to discuss your needs and schedule an estimate.
Aesthetics
Concrete contractors strive to strike a delicate balance between functionality and aesthetics. They use the concrete industry’s best practices to ensure that their work meets both standards. This includes selecting the correct type of concrete for each project, which helps avoid problems such as excessive shrinkage or cracking. They also use advanced finishing techniques to enhance the aesthetics of a concrete project. For example, they can use integral pigments to add color to the concrete, or they can apply decorative stamping and printing techniques that mimic natural stone or other materials.
In addition, they have extensive knowledge of local zoning laws and building permits, which helps them avoid costly fines and delays. They also use professional-grade equipment to complete each project quickly and accurately. This is important because a delay in completing the project can lead to additional expenses and frustration for both homeowners and contractors.
When choosing a concrete contractor, it’s essential to ask the right questions. Verify their credentials, examine their portfolio, and discuss costs and timelines. It’s also helpful to inquire about their safety protocols and quality assurance measures. Additionally, it’s a good idea to assess their communication style and schedule regular check-ins with them throughout the project.
Masonry contractors build structures with a variety of materials, including bricks, stones, and cement blocks. They use mortar to hold these elements together, creating durable and visually appealing concrete structures such as patios and walls. In addition to installing these structures, masonry contractors can also repair them when needed.
Before a concrete project can begin, the contractor must prepare the site by clearing away debris and ensuring that the area is level. They may also use forms or reinforcements to shape the concrete and prevent unwanted voids or bumps. Once the concrete is poured, it must be allowed to cure properly. This process usually takes 28 days and is crucial for the structural integrity of the concrete.
After the concrete has cured, it’s time to finish it. This involves adding any desired textures or patterns to the surface, which can make it look more attractive and create a unique visual experience. This stage also includes staining or painting the concrete to protect it from weathering and other damage.