When you drink from a plastic water bottle, use a toothbrush or get into your car, chances are the product was made using plastic injection molding. American Plastic Molds specialize in this complex process, and we know how to make it work for you.
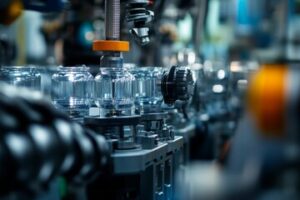
Family molds are ideal when you need to create several identical parts at once. They are also useful when you need to incorporate features like bosses for threaded inserts, friction fits as joining features or living hinges.
Plastic extrusion is the process of pushing melted plastic through a die to give it a desired shape. This method is used to make products like pipes, drinking straws, curtain tracks and rods. Extrusion is a high volume manufacturing technique, and it is also more cost effective than injection molding. However, it has some limitations when it comes to the variety of shapes you can produce with it.
The main components of an extruder include a feeder, hopper, breaker plate, barrel, feed pipe/adapter, and die. These elements work together to facilitate the efficient melting, shaping and cooling of the molten plastic. The hopper is where the plastic granules are stored, and from there they are fed into the barrel. The barrel is heated to melt the granules into a uniform liquid, and it is fed through a screen pack and breaker plate to filter out any contaminants. The melted plastic then travels through the feed pipe/adapter and into the die. The die gives the molten plastic its desired shape, and it is then pulled and cooled.
A blown film extrusion die is a vertical cylinder with a circular opening. A roller system is used to force a hot molten plastic film upward through the die, and an air ring around the die helps to cool it. The resulting product is a thin and solid plastic sheet with an excellent elongation property. This makes it perfect for insulating cables.
During the extrusion process, there are several factors that can lead to problems. These include:
The most common type of plastic in extrusion is polyethylene. This is a strong and durable material that is resistant to abrasion, impact, chemicals and weathering. It is also highly recyclable. Another common type of plastic in extrusion is acrylonitrile butadiene styrene (ABS). This is a tough and rigid material that is resistant to impact, abrasion, heat and corrosion. This type of plastic is commonly found in automobile body parts, insulation and packaging. It can also be found in many other industrial applications, including furniture and electrical wires. It is often combined with other materials to improve its performance and durability, such as glass fiber or metal.
Rotary Moulding
Rotational molding, also known as rotomolding, is a method of plastic forming that involves heated and slowly rotating a hollow mold with powdered plastic (like polyethylene) inside in various directions. This heat melts the plastic powder and sticks it to the interior walls of the mold, which then solidifies into its chosen shape. The molded product is then allowed to cool. As it does so, the new product shrinks slightly, which helps make it easier to remove from the mold.
The rotary molding process is slow in comparison to other high-speed, high-pressure plastic forming methods, but it’s effective for creating hollow one-piece construction products and for producing items that need to maintain their shape after cooling. It’s particularly well-suited to making thermoplastic materials that have a high thermal stability, such as polyethylene. It’s also a good choice for producing replacement parts for broken metal products.
This method replaces injection pressure with holding pressure, which helps to compact the molten plastic and ensure the integrity of the finished product. A runner system is used to convey the plastic from the nozzle into the mould. After the plastic has been molded, it’s removed from the mold and the mold is bolted shut ready for the next cycle.
Unlike other plastic-forming processes, rotational molding produces minimal scrap and uses relatively low energy to produce parts. It’s also a good option for producing high-quality, attractive-looking products. In fact, it’s often chosen for aesthetic applications that require smooth surfaces and rounded edges. A wide range of finishes and colors can be applied to rotomolded plastic, and it’s possible to include prefinished features in the mold such as metal threads, internal pipes or structures, logos, slots, and other features.
Since the rotomolding process is slower than other types of injection molding, it’s typically more efficient on a smaller scale. It’s also a good choice when it comes to producing larger products and parts with complex shapes. However, it’s important for manufacturers to carefully consider how their rotary-molded products will be used in order to determine optimal wall thicknesses that balance functional requirements with material costs.
Continuous Moulding
This method of plastic molding involves the injection of molten polymer into a pre-made mold. This is a very popular process and can be used for a wide variety of projects. It’s also a very efficient method of producing multiple parts. This is because of the high-volume production capabilities that it offers. However, due to the complexity of the molds that are required, this is a process that’s typically best suited for larger parts.
This process can be utilized to make plastic products with a very specific shape and size, and it’s also highly effective at creating very complex geometrical shapes. The injection molding process has a very high tolerance level and can be used for a wide range of different materials. This includes thermoplastics as well as thermosets.
Injection molding is also one of the most cost-effective ways to produce plastic parts in high quantities. This is because the initial design and construction costs associated with this type of molding are lower than that of other types of plastic molding. It’s also an ideal choice for producing parts that require a very tight fit.
Another common method of plastic molding is known as extrusion. This is a form of plastic molding that involves forcing hot raw material through a custom die to create a continuous product. It can also be utilized to create a linear product with a fixed cross-sectional profile, such as PVC piping and drinking straws (coextrusion). Extrusion is often utilized for parts that need to have a very durable, long-lasting surface finish.
As this plastic molding technique produces a linear part, it can help reduce the total number of manufacturing steps required. This can lead to significant cost savings, as well as environmental benefits.
Unlike other forms of plastic molding, the continuous casting process does not use a solid starting bar. Instead, a melted batch of metal is placed into a tundish that acts as a reservoir. From there, the molten metal is fed into a casting mold. Various cooling systems can be implemented to help improve the quality of the final product. For example, an electromagnetic induction heating system can be used to minimize the effects of thermal stresses on the casting. This can also help reduce the need for costly machining and other post-casting processes.
Pressure Moulding
The pressure moulding method involves a compression mold that shapes the thermoplastic material. It is a low-pressure process, typically used for medium to high volume production runs and it can produce parts with complex geometry and fine surface details. It can also produce textured or glossy finishes that are difficult to achieve with vacuum forming. The process can even create fine radii and sharp corners that are not possible with traditional vacuum forming.
Several different types of pressure are involved in the plastic molding process, including clamping, injection, and holding pressures. Correctly balancing these forces is key to creating consistently good parts. Getting this right requires an understanding of the processes and equipment. It is also important to understand the impact of these pressures on the quality of your final product and cycle times.
Clamping pressure is the pressure required to seal the mold and prevent the thermoplastic material from leaking out during the injection phase of the molding process. Injection pressure is the pressure that forces the hot plastic into the mold cavity to shape it. When the injection pressure is too high, it can damage the injection mold. This can lead to flash, over-filling, stress concentrating near the injection gate, and dimensional instability in the finished part. Injection pressure must be scaled back quickly when the injection molding machine senses the changeover point, which is when it reaches 95% of its total volume.
The pressure molding process can be used to produce a wide variety of polymers, including thermosets, thermoplastics, and rubbers. The raw materials must be cleaned, cut, and preheated to ensure that they are of the proper size and consistency. This step is particularly important when working with brittle materials that are susceptible to cracking and warping during the injection process. It is also critical to optimize the mold design for proper flow of the material and efficient cooling, as well as to prevent air entrapment.
After the injection phase, the mold must be ejected from the injection chamber and allowed to cool before being inspected for defects and ready for a second injection. Depending on complexity and volume, this can be done manually with handheld trimming tools or automatically with an automated system that uses a plunger-style ejector pin that telescopes from the bottom of the mold.